EV普及のカギを握るか? 全固体電池開発事情
公開: 更新:
「報道部畑中デスクの独り言」(第349回)
ニッポン放送報道部畑中デスクのニュースコラム。今回は、全固体電池の開発事情について---
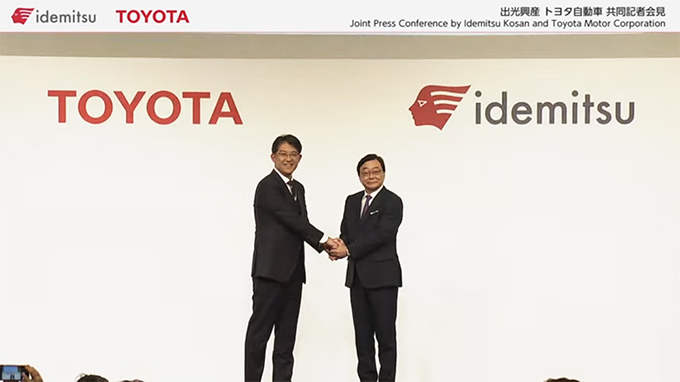
画像を見る(全4枚) トヨタ自動車・出光興産 共同記者会見(左:トヨタ・佐藤社長、右:出光・木藤社長)(オンライン画面から)
今秋開催されたジャパンモビリティショー。日本自動車工業会の集計では来場者数が111万2000人でした。目標の100万人を超え、関係者はほっと胸をなでおろしているかと思います。
ところで、ショーの見どころのひとつに電気自動車「次世代EV」がありました。小欄でもお伝えした通りです。動力源はそれだけでなく、各社さまざまな提案をしていましたが、やはり電動化、EV化の流れは早かれ遅かれ、止まることはないでしょう。
そして、その普及のカギを握るのは電池。なかでも注目は全固体電池です。以前も小欄で取り上げてきましたが、あれから約2年半、現状について掘り下げます。
「全固体電池にいま会社の資源を集中して研究開発を進めている。ここがゲームチェンジングのポイントになるだろう。全固体電池が入ることによって航続距離は圧倒的に伸びる。充電時間も減る。いろいろな場所で充電が早くできることになると、ここからお客様の感覚は変わっていくと思う」
モビリティショーで日産自動車・商品企画部の成田豪史さんは将来を展望しました。
この全固体電池、リチウムイオンバッテリーの一種で、一言で言いますと、電解質を液体から固体に置き換えたものです。電解質は溶媒に溶解した際に、陽イオンと陰イオンに電離する物質です。電気を通すための「橋渡し」の役目を持ちます。
リチウムイオンバッテリーそのものは自動車のみならず、パソコンや携帯電話でもおなじみで日常生活には欠かせませんが、これは現状、ほとんどが液体系と言われる電解質が液体の電池です。通常の使用では問題ないよう対策は施されているものの、液体である以上、液漏れの可能性はゼロではありません。
また、対策が不十分であったり、誤った使い方をすると、最悪発火する可能性もあります。作動環境の範囲は限られ、温度でみた作動範囲は現状の液体系はマイナス20~60度ぐらいとされています。電気自動車もバッテリーを保護するために、ヒーターが組み込まれていたりします。これが全固体電池だとマイナス40~120度、水が沸騰する温度でも耐えられることになります。温度変化に強いのが特徴の1つです。
さらに、全固体電池にはさまざまな利点があります。モビリティショーに先立つ10月12日、トヨタ自動車と出光興産が全固体電池の開発に関し、協業することが発表されました。
「クルマの未来を変えていく。そのカギを握るのは自動車産業とエネルギー産業の連携。両者の力を1つにして全固体電池を量産化し、日本発のイノベーションを実現する」(トヨタ・佐藤恒治社長)
「全固体電池の実用化に挑むトヨタの実現力を、出光は材料である固体電解質の製造・量産を通じ、技術で支えていく。クルマの未来を変えていくことは、エネルギーの未来も変えていくこと」(出光・木藤俊一社長)
全固体電池は、前述の温度変化の強さの他に、エネルギー密度の高さも特徴です。航続距離は現在のEVの2倍以上、1000kmを超えると言われています。また、同じ性能であればよりコンパクトにできるということで、さまざまな車種への展開が期待されます。
「クルマにおけるいくつかの大きなパラダイムチェンジ(ものの見方の変化)があると思う。パッケージの自由度がより上がり、低重心で、キャビンスペースに多くのスペースを取ることができる」(トヨタ・佐藤社長)
一方、全固体電池ではいくつかの課題もあります。その1つが耐久性です。充放電を繰り返すと、正極・負極の固体電解質の間に亀裂ができ、電池性能が低下するのだそうです。トヨタの佐藤社長は課題を克服し、「割れにくく高い性能を発揮する材料を開発することができた」と胸を張りました。今回の記者会見の意義の1つです。
固体電解質の中身、成分そのものは「秘密のレシピ」と言えるもので、ベールに包まれているところも少なくありませんが、会見では柔らかく、密着性の高い=はがれにくい材質の開発に成功したことが明らかにされました。電池開発の関係者によれば、これまでの固体電解質に、別の電解質を加えることで柔らかくしたものではないかと推測されます。
これはお菓子の「おこし」に例えられます。そのままだと硬いけれど脆い。これが亀裂や割れやすさにつながっているわけですが、おこしの隙間にゼリーのような別の固体電解質を流し込む形にして固めると、多少の衝撃では割れない状態になります。また、ゼリーが緩衝剤となり塑性変形の自由度も増す……加工がしやすくなるわけです。
全固体電池が加工しやすくなるとどうなるか……例えばシート状にもできると言われています。そうなりますと、確かにさまざまなクルマに対応できそうです。モビリティショーでトヨタや日産がスポーツカーからミニバン、SUV、ワンボックスといろいろなコンセプトカーを出展したのは、将来さまざまなクルマができる、クルマが見たこともない形になる……そんなメッセージだと私は感じました。
また、全固体電池を語るに欠かせないのが電解質の種類です。大きく分けて「硫化物系」と「酸化物系」の2つがあります。
「硫化物系」はリチウムイオンを通しやすい特性を持ちます。つまり、導電性が高く、性能を高くすることにつながります。一方、水分を吸うと有毒ガスである硫化水素が発生するため、製造工程や製品には高い防水性を持たせる必要があります。
「酸化物系」はこうした有毒ガスは発生しませんが、陶器のように何百度もの高温で焼結するという高い加工技術を必要とします。これにはコストや時間がかかり、自動車のような大量生産には向かないとされています。
トヨタと出光が開発している全固体電池は「硫化物系」ですが、ここでモノを言うのが、出光です。出光はオイルショック後、石油に代わるエネルギーを模索していました。そのなかで、石油の精製過程で発生する、いわば「副産物」の硫黄に目をつけ、今回の固体電解質の開発にこぎつけました。トヨタが出光とタッグを組んだのは、まさにこんな背景もあるわけです。硫化物系の課題についても担当者は自信を見せていました。
「材料・電池・アセンブリ・電池システム、クルマ全体、四重の安全システムをいま検討し、メドはついている」(トヨタ・海田啓司カーボンニュートラル先行開発センター長)
「材料そのもの、いわゆる硫化水素の発生を抑えるというものを設計のなかに組み入れる。ゼロにはできないが、できるだけそこに配慮した形の材料設計を今後ともやっていく」(出光・中本肇常務)
全固体電池のさまざまな利点、課題についてお伝えしましたが、さらに固体電解質に関しては、薄く均一に加工したり、精密に“塗る”ことが求められます。以前こうした加工には大規模なプレス技術が必要でしたが、電池開発の関係者によれば、最近は「ロールtoロール」という、ロール状の基板に連続して印刷するような形で、電極を塗る方式も確立されつつあります。
ただ、こうした技術は加工する装置も含めて、まさに「ノウハウ」の塊。こうしたノウハウが流出しないよう注意しながら、それらを安く、安定してつくらなくてはいけない……量産技術が求められます。
「実証ベースの研究開発には一定のめどが立った。量産化の壁を超えていくための挑戦をこれからやっていく。できれば2027年、2028年の初頭までには世の中にお届けできるようにペースを上げていきたい」
トヨタの佐藤社長は今後についてこのように意気込みます。
リチウムイオンバッテリーを開発したノーベル化学賞受賞者の吉野彰さんも話していましたが、新たな事業を立ち上げるときには、3つの壁が立ちはだかると言われています。研究から開発につながる際の壁「魔の川」、開発から製品化、実用化につながる際の壁「死の谷」、そして、製品の市場投入から産業としての確立に至る際の壁「ダーウィンの海」です。
電池開発の関係者は、「現在は死の谷を超えた段階」と分析しますが、目指す全固体電池の実用化時期は、トヨタが2027~2028年にかけて、日産が2028年。液体系の改良も進むなか、壁を乗り越えるにはこの年月は長いでしょうか? あっという間でしょうか?
「シェアという意味では遅れているという言い方になる。ただ、技術力では決して遅れていない」
日本の自動車産業としてのEVの国際競争力について、日本自動車工業会の豊田章男会長(トヨタ自動車会長)は以前、このように話していました。全固体電池開発の進捗、豊田氏の発言はある種の自信とも言えるのかも知れません。(了)